Molybdenum and its alloys, with high melting points, excellent corrosion resistance and high temperature creep resistance, are a vital high-temperature structural material. However, the poor oxidation resistance at high temperatures is a major barrier to their application.
1. Introduction
Molybdenum and molybdenum-based alloys have a high melting point (2620 °C), good high-temperature mechanical properties and high conductivity and thermal conductivity, and are widely used in high-temperature structures [1][2][3][4][5][6][5,6,7,8,9,10]. However, the alloys have a poor oxidation resistance, and the “Pesting oxidation” at 400–800 °C and oxidation decomposition above 1000 °C are the main factors that limit their application [7][8][9][10][11,12,13,14]. At present, the alloying and surface-coating technology are the main methods to increase the oxidation resistance of the basal materials [11][12][15,16]. The types of molybdenum alloys and the various surface coating technologies of Mo and its alloys are shown in Figure 1 [13][14][15][16][17,18,19,20]. It can been seen that the Ti, Zr, W, Re, Si, B, Hf, C and rare earth oxides are often added to pure Mo as beneficial elements to prepare molybdenum alloys. However, the result of alloying is not satisfactory when considering the mechanical properties and high-temperature oxidation resistance of the alloys [17][18][21,22]. For example, adding a certain amount Ti element to the alloy can enhance its strength, but it will further accelerate the oxidation of the alloy [19][23]. Mo–Si–B alloys have satisfactory high temperature oxidation resistance, but their fracture toughness is poor. Mo–Ti–Si–B alloys are considered as a promising ultra-high temperature material. However, their oxidation resistance and mechanical properties need to be further studied [20][24].
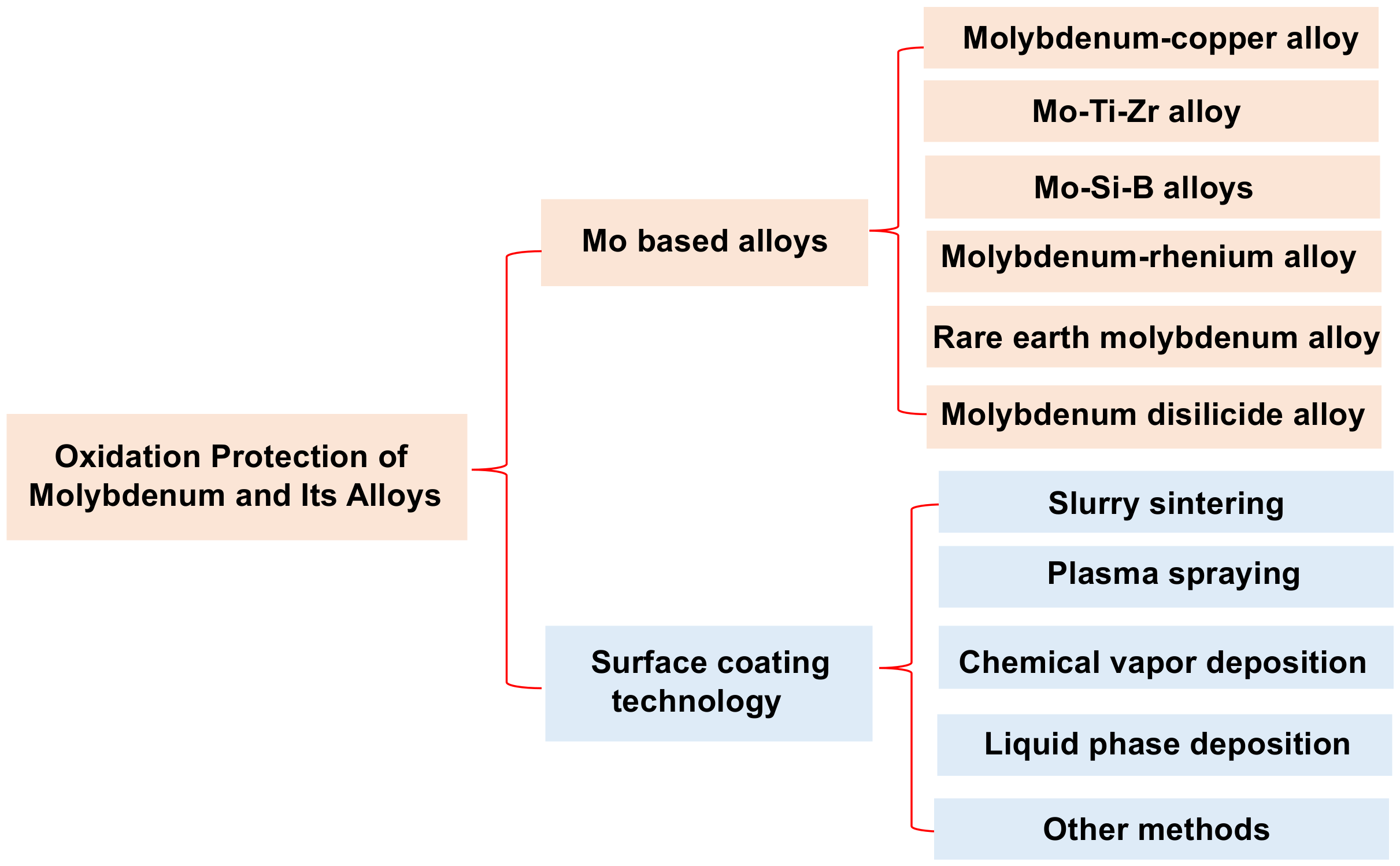
Figure 1. Overview of Mo alloy types and Mo and its alloy surface-coating technology.
2. Microstructure and Oxidation Behavior of Coatings
2.1. Coatings Prepared by Slurry Sintering (SS)
2.1.1. Microstructure and Growth Mechanism of SS Coatings
The slurry sintering (SS) method mixes alloy or silicide powder with binder in a certain proportion and then dissolves it in organic solvent to obtain the mixture. The mixture was evenly coated on the surface of the substrate, and then heated for a certain time in vacuum or Ar atmosphere, so that the substrate and mixture could be fully combined to form a coating on the surface
[21][22][41,42].
2.1.2. Oxidation Behavior and Mechanism of SS Coatings
It is observed that an oxide layer forms on the surface of SS coatings after oxidation, which is mainly composed of SiO
2, TiO
2, Mo
5Si
3, etc. Compared with the original coating, the thickness of the oxidized coating increases significantly, which is due to the volume of the coating expanding and the interface migration caused by the inter-diffusion reaction. However, the thickness of the MoSi
2 layer decreases significantly due to the growth of the oxide film and the migration of the interface layer. By contrast, the interdiffusion between the coating and the substrate becomes more sufficient with the increase of exposure time, resulting in a significant increase in the thickness of the interface layer dominated by Mo
5Si
3 [23][24][25][26][43,44,45,46].
2.2. Coatings Prepared by Plasma-Spraying Technique
2.2.1. Microstructure and Growth Mechanism of Plasma-Spraying Coatings
The plasma-spraying technique is one of the most widely used coating preparation in thermal-spraying technology. Its principle is heating and ionizing a certain gas (N
2, H
2, Ar, He or their mixture) by an electric arc. The generated high-energy plasma arc can heat powdery materials to molten or semi-molten state and spray them onto the substrate surface at high speed to form a coating
[27][28][29][54,55,56]. Among them, the air plasma spraying technique (APS), plasma-transferred arc (PTA) and spark plasma sintering (SPS) are widely used in the surface oxidation protection of Mo and its alloys.
2.2.2. Oxidation Behavior and Mechanism of Plasma-Spraying Coatings
It should be noted that except for Mo
2BC coating, the mass of the other coatings increases compared with that before oxidation. This is mainly due to the strong affinity force between C and oxygen. During oxidation, the volatilization rate of CO is greater than the formation rate of B
2O
3, resulting in the reduction of the overall quality of the coating.
2.3. Coatings Prepared by Chemical Vapor Deposition (CVD) Technology
2.3.1. Microstructure and Growth Mechanism of CVD Coatings
The principle behind chemical vapor deposition (CVD) technology is the process of using gaseous substances reacting with a solid substrate to generate solid deposits
[30][31][69,70]. The process conditions and mechanical properties of the oxidation-resistant coatings prepared on molybdenum by the CVD technique as shown in
Table 16 [32][33][34][35][36][71,72,73,74,75].
Table 16.
Summary of process, composition and properties of CVD coatings on Mo surface.
Substrate |
Composition of Gas Mixture |
Process Conditions |
Composition and Thickness of Coatings (µm) |
Bond Strength (MPa) |
Hardness (GPa) |
Surface Grain Size (μm) |
Refs. |
Gas Flow Rate (ml·min | −1 | ) |
Deposition Temperature (°C) |
Deposition Time (h) |
Outerlayer |
Interface Layer |
Mo |
SiCl | 4 | , H | 2 |
SiO | 2 | (3.00)SiCl | 4 | : 50.00 H | 2 | : 100.00 |
MoSi620.00 |
2 | (5.00)3.00 |
SiO |
1000 °C, 3.00 h |
- | 2 | (3.00) |
SiO | 2 | , MoOMoSi | 2 | (5.00) |
- |
3 | - |
15.00 |
MoSi | 2 | -Mo | 5 | Si | 3[32] | [71] |
12.00 |
[ | 32 | ] | [ | 71 | ] |
NH | 3 | , SiCl | 4, | H | 2 |
MoSi | 2 | -Si | 3 | N | 4 | (72.00)NH | 3 | : 100.00 H | 2 | : 990.00 SiCl | 4 | : 10.00 |
1100.00 |
Mo | 2 | N (5.00)NH | 3 | : 2.00 SiCl | 4 | : 5.00 |
MoSi | 2 | , Si | 3 | N | 4 | (72.00) |
500 °C, 1492.00 h |
1.00 h cycles |
Si | 2 | ON | 2 | Mo | 2 | N (5.00) |
- |
, SiO | 2 | , MoO | 3 | Mo | 4 | O | 11 | , Mo | 9 | O | 26 | , (3.00) |
MoSi | 2 | -Si | 3 | N | 4 | (100.00)- |
3.00 × 10 | −1 |
5.00 × 10 | −1 |
[33] | [72] | [33] | [72] |
BCl | 3 | , TiCl | 4 | , H | 2 |
BCl | 3 | : 195.00 TiCl | 4 | : 130.00 H | 2 | : 635.00 |
1000.00 |
2.00 |
TiB | 2 | (13.00) |
TiB | - |
7.00 |
28.00 |
2.00 |
2 | (13.00) |
- |
900 °C, 6.00 h |
- |
TiO | 2 | , B | 2 | O | 3 |
- |
8.00 × 10 | −2 |
[34] | [ | [34] | [73] |
73 | ] |
WCl | 2 | , H | 2 |
- |
1800.00 |
2.00 |
W (160.00) |
- |
- |
- |
TiB | 2 | (13.00) |
- |
450 °C, 5.00 h |
- |
TiO | 2 | , B | 2 | O | 3 | 20.00 |
- |
3.00 × 10 | −2 |
[37] | [78] | [35] | [74] |
CH | 4 | , SiCl | 4 | , H | 2 |
CH | 4 | , H | 2 | :200.00 SiCl | 4 | : 10.00 H | 2 | : 990.00 |
1200.00, 1100.00 |
CH | 4 | : 65.00 SiCl | 4 | : 10.00 |
SiC, MoSi | 2 | (60.00) |
MO | 2 | C (25.00) |
- |
- |
3.00 × 10 | −1 |
[36] | [75] |
2.3.2. Oxidation Behavior and Mechanism of CVD Coatings
Table 27 shows the microstructure evolution and mass gain of CVD coatings before and after oxidation under different conditions. Obviously, researchers mainly reported the oxidation of the coating at low temperature (500 °C to 1000 °C), and the oxidized coatings mainly consist of an oxide layer, intermediate layer and interface layer
[32][33][34][35][36][37][71,72,73,74,75,78].
Table 27.
Microstructure evolution and mass gain of CVD coatings on molybdenum before and after oxidation.
Substrate |
Composition and Thickness of Coatings (µm) |
Exposure |
Comments |
Composition and Thickness of Oxidized Coatings (µm) |
Mass Gain (mg·cm | −2 | ) |
Refs. |
Outer Layer |
Interface Layer |
Oxide Layer |
Intermediate Layer |
Mo |
W (160.00) |
W/Mo (2.00) |
- |
- |
- |
- |
- |
[ | 35] | [74] |
MoSi | 2 | -SiC (60.00) |
MO | 2 | C (25.00) |
500 °C, 1492.00 h |
1.00 h cycles |
SiO | 2 | , MoO | 3 | Mo | 4 | O | 11 | , Mo | 9 | O | 26 | (8.00) |
MoSi | 2 | -SiC (80.00) |
1.00 × 10 | −2 |
[36] | [75] |
3. Conclusions
During slurry sintering, due to volatilization of solvent and binder, the prepared coating has poor surface quality and high porosity. Reducing sintering temperature and prolonging sintering time can optimize coating structure and improve coating quality to a certain extent. The lower process temperature of CVD makes the preparation efficiency of the coating low and the preparation time long. However, the technology is suitable for workpieces with complex shapes and the coatings obtained have a good low temperature oxidation resistance. In contrast, plasma spraying and the hot-dip silicon method presented a high deposition efficiency due to high diffusion temperature. After 5 to 25 min of treatment, coatings several tens to several hundred microns thick can be obtained on the substrate surface. However, the plasma-spraying coatings have a high surface roughness and porosity because the spraying material is still mixed with a small quantity of residual gas and solid particles. It is worth noting that liquid-phase deposition coatings have a dense and smooth surface. This is conducive to the formation of protective oxide film on the coating surface in the oxidation process. However, the structure of the coatings are relatively simple, and the oxidation resistance of the coatings needs to be further studied. In addition, the molten salt method and laser-cladding technology have also been widely applied in the preparation of oxidation protective coatings on Mo and Mo-based alloys.