Metal sulfide precipitation can efficiently recover several metals and metalloids from different aqueous sources, including wastewaters and hydrometallurgical solutions.
1. Introduction
Metal sulfide precipitation is studied because it is a process that is applied to recover or remove metals and metalloids from industrial effluents or hydrometallurgical leachates. This process uses a sulfide source, typically H
2S, Na
2S, CaS, (NH
4)
2S, or NaHS to react with a cation contained in an aqueous solution, according to the reaction mechanism described in Equations (1)–(4)
[1]. Metal sulfides have low solubility (
Table 1) with respect to other precipitates such as hydroxides
[2]. This characteristic is very attractive for environmental purposes, particularly when a dangerous heavy metal is removed and disposed of safely, because it is less likely to be leached in a wide pH range. In addition, a high pK
sp value translates into a favorable tendency for Equations (3)–(4) to form products, showing a high conversion and, consequently, an efficient precipitation process.
Table 1. Solubility products (pK
sp) at 25 °C for selected elements. Adapted from
[2].
Element |
pKsp |
Bi3+ |
98.8 |
Hg2+ |
52.2 |
Ag+ |
49.2 |
Cu+ |
47.7 |
Cu2+ |
35.9 |
Cd2+ |
28.9 |
Pb2+ |
28.1 |
Sn2+ |
27.5 |
Zn2+ |
24.5 |
Co2+ |
22.1 |
Ni2+ |
21.0 |
Fe2+ |
18.8 |
Mn2+ |
13.3 |
Metal sulfide precipitation is naturally appealing for research, which can include the removal of potentially toxic elements (metals and metalloids) from industrial effluents, such as acid mine drainage (AMD) or copper smelter wastewater, and for recovering valuable metals from leachates of hydrometallurgical plants treating ores, wastes, or tailings. Likewise, the application of this method has improved for different metals, such as copper, cobalt, and nickel or metalloids such as arsenic.
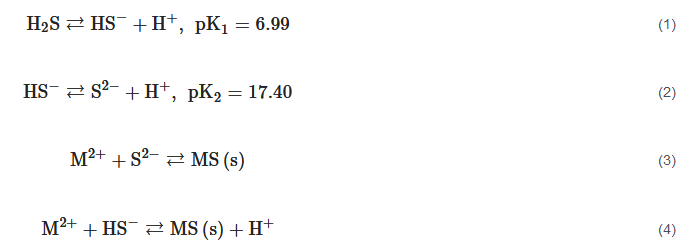
In 2010, a crucial review article published by Alison E. Lewis
[1] consolidated the background and improvements in the field. From that date onward, studies on metal sulfide precipitation have expanded to different applications, and the number of articles related to the precipitate characteristics and solid–liquid separation improvements have also increased. Moreover, there is more industrial experience of sulfide precipitation-based processes in the last decade, particularly considering the SART (Sulfidization, Acidification, Recycling, and Thickening) process, which recovers copper and cyanide from cyanide leachates solution in gold cyanidation
[3], and the copper recovery from Acid Mine Drainages (AMD)
[4].
The general flow diagram of a typical metal sulfide precipitation process is shown in Figure 1.
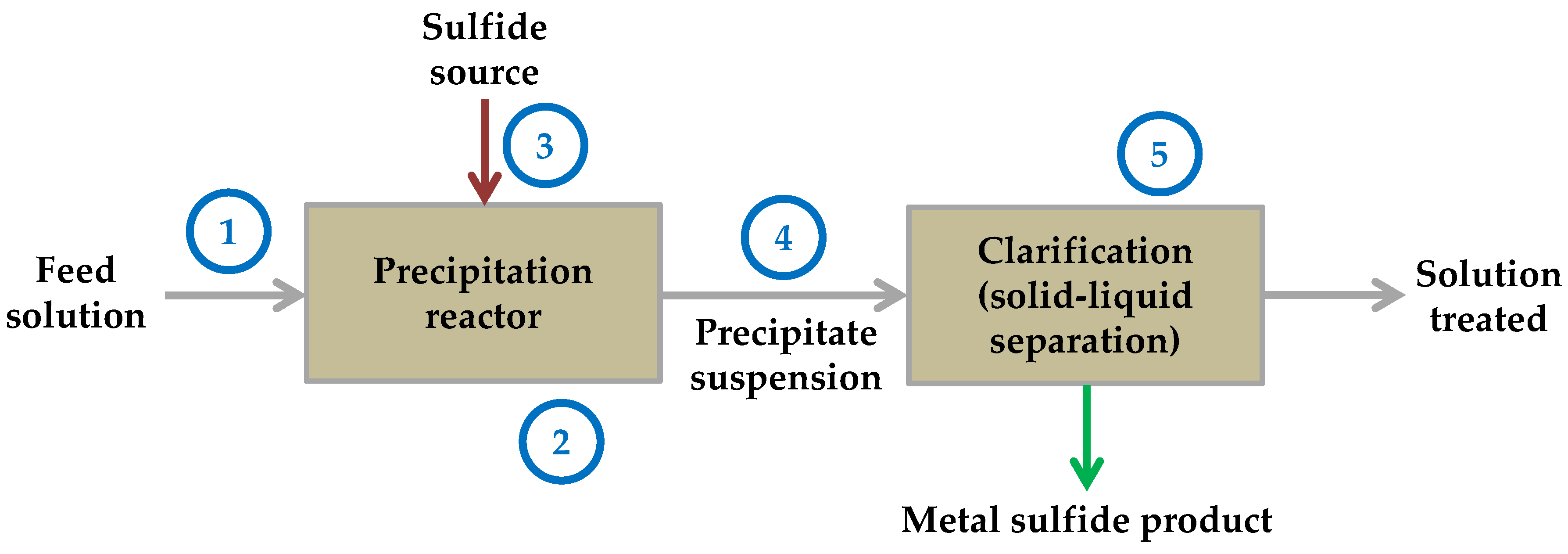
Figure 1. Schematic representation of the flow diagram of a typical metal sulfide precipitation process. Numbers are related to the focus of the studies reviewed here.
2. Latest Breakthroughs in Solid-Liquid Separation
As discussed in the previous section, the particle behavior of sulfide precipitates is determined by its hydrophilicity/hydrophobicity capacity, the ions contained in solution, the sulfide concentration, and pH. This situation imposes high variability of the
particle PSDsize distribution (PSD) that results from the reaction stage, increasing the uncertainty of solid–liquid separation performance. At an industrial scale, the current equipment used to separate precipitates are conventional gravitational clarifiers, as used, for example, in the SART process
[3] and for the treatment of AMD
[4]. Although these industrial applications have reported to be successful, they are still limited to the recovery of a few metals, mainly copper. Furthermore, there are several opportunities to improve these results, such as the size reduction, minimization of solid losses in the overflow, and the process control
[5]. In this regard, there are critical studies that showed the fragility of the overall process of recovery with respect to a correct control of the clarifier, losing even 40% of copper recovery in this stage
[6].
Studies to optimize the solid–liquid separation in metal sulfide precipitation processes are still emerging, although there are a few interesting examples which could address new research trends. The use of a magnetic field to modify the zeta potential of particles
[7], the use of an abiological granular sludge
[8], and the use of
Ultraviolet (UV
) light irradiation to improve the aggregation
[9] have been experiments conducted to enhance the settling rate of particles. In the first case, the application of a magnetic field of 2T for 40 min increased the zeta potential from −40 mV to 16.5 mV. This result indicates that the aggregation of particles could increase after applying a magnetic field, but no PSD or settling test were performed
[7]. In the second case, the use of an abiological granular sludge (ABGS) was used to improve the aggregation and settling of sulfide precipitates. Results showed that the use of an ABGS allowed for a settling velocity of 3.4 m/s for Zn/Pb precipitates from a real wastewater
[8]. Finally, the third case showed that the particle size of CdS and a mix of CuS/CdS increased from 1–5 µm to 1000 µm after 30 min of applying UV light irradiation. Moreover, the zeta potential increased between 120% and 150% for both types of sulfide precipitates
[9]. Thus, the results of these studies are interesting to improve the settling rate of a gravitational clarification stage, although the industrial scaling-up and implementation could be challenging, particularly in the case of magnetic field or UV light irradiation applications.
In terms of the development of new solid–liquid separation processes or equipment, the gravitational lamella clarifiers have been conceptually proposed
[10], but no data or results have been provided. A gravitational field-flow fractionation (GFFF) tank was proposed and designed using Computational Fluid Dynamics (CFD) simulations to fractionally separate CuS, ZnS, and As
2S
3, obtaining interesting results to separate particles according to their size
[11]. There were no validation studies of the model and design with experimental results.
Recent applications of membrane filtration processes, specifically microfiltration (MF), to clarify copper sulfide precipitates produced in cyanide media
[12] and AMD
[13] have been reported (
Figure 2). Furthermore, a mix of copper and zinc sulfide from a real cyanide solution of a gold mine was processed by MF
[14]. Using feed pressure of slurries slower than 2 bar, flux values of 0.1 to 1.4 L/m
2s were reached for copper sulfide and Cu/Zn sulfides in cyanide media
[14][12] and 0.1 L/m
2s for copper sulfide in AMD
[13]. The lowest flux for cyanide media was reached for a low copper concentration (200 mg/L) or under the presence of Zn, a fact that in both cases can be explained by the small particle size generated in the reactor. These flux results meant a reduction in the residence time from 60–90 min to less than 5 s with respect to conventional gravitational clarifiers
[12]. Consequently, there was also a reduction of 90% of equipment volume and around 30% of capex compared to conventional processes
[14]. In the case of cyanide solutions, the use of membrane filtration processes also minimizes the emanations of HCN to the environment. Therefore, the use of this alternative process as a solid–liquid separation stage could not only support the overall recovery of the process, but it could also reduce the capital costs.
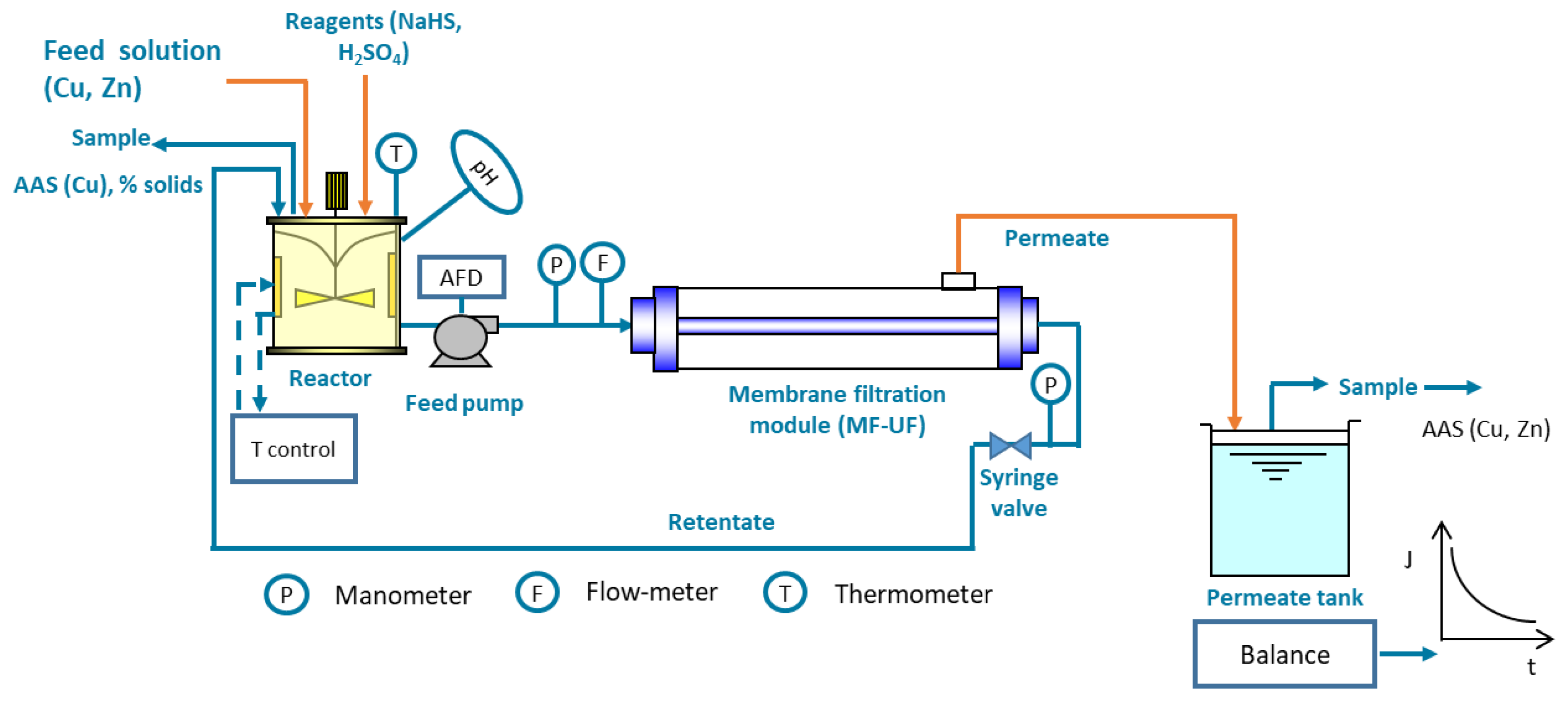
Figure 2. Membrane filtration prototype at a laboratory scale applied to assess metal sulfide precipitates in cyanide media and AMD. Adapted from
[12].
3. Future Perspectives
Scientific and industrial applications of the metal sulfide precipitation process show that this it is a promising alternative to remove or recover potentially toxic elements (metals or metalloids) from different sources. Nevertheless, there are several gaps in our field, which are primarily due to a lack of understanding of this method with the aim of optimizing and expanding its application. This section summarizes an overview of challenges that should be addressed in further studies.
3.1. Selective Precipitation and Recovery
One of the main challenges is the control and establishment of the operational conditions required to advance towards the selective separation and recovery of highly pure metal sulfide precipitates from polymetallic sources, such as AMD, refinery wastewater,
pregnant leach solutions (PLS
), and others. The high variability of metal concentrations and their ranges present a challenge in terms of control. The control of pH and Eh, and K
sp [15][16][17][18] are key variables to control a selective precipitation. These studies might support future methods for control strategies and the definition of the number of stages.
3.2. Kinetic Studies
This subject has been scarcely addressed, even when there are different studies showing long reaction times
(see Table 3). Likewise, when H
2S gas is used, establishing the controlling stage of process velocity should be considered
[19]. The first order model proposed by Yang and colleagues
[20] was determined using a small quantity of experimental data and is limited to CuS. Through this process, the correct design of reactors should be based on proper kinetic models for each specific application.
3.3. Reactor Type and Supersaturation Control
Different reactor types that differ operationally from the conventional CSTR have been proposed, mainly focused on controlling the supersaturation
[21][20][22]. The supersaturation control can promote the generation of precipitates with larger particle size to improve the solid–liquid separation
[22]. However, recent studies show the relevance of the hydrophilicity/hydrophobicity capacity of metal sulfides
[23][24][25], which demonstrate that the supersaturation control is not the unique variable that affects the PSD of precipitates. In fact, the aggregation time should be considered alongside with the reaction time when designing the reactor. The recent study performed by Barros and colleagues
[26], using the FBRM, showed that the aggregation time was higher than the reaction time required to reach a maximum and stable particle size. Therefore, the optimal solid-liquid separation process strongly depends on the residence time defined for the reaction stage.
Novel methods to control the supersaturation, and also the sulfide consumption, could be conducted to advance in the development of new materials which could allow for the controlled release of sulfide
[27].
3.4. Solid-Liquid Separation
During the last decade, several studies have tried to understand the behavior of precipitates to design an optimized solid–liquid separation stage. The main conclusions are that the aggregation behavior strongly depends on the hydrophilicity/hydrophobicity capacity of metal sulfides, affecting the resulting PSD during the precipitation
[23][24][25]. However, the PSD curves of hydrophobic and highly aggregated precipitates, such as copper sulfide, show a bi-modal behavior, even containing up to 30% of particles smaller than 10 µm
[28][26]. These fine particles can remain disaggregated due to the supersaturation condition or the formation of oxidized species on the particles’ surface, diminishing the aggregation capacity
[26]. The fine and colloidal particles can thereby be more exposed to the solution characteristics, such as pH, sulfide concentration, or ionic strength
[29][30]. Hence, a deeper understanding of the reaction conditions that define the PSD of precipitates will be necessary for each system in order to optimize the solid–liquid separation process.
The development of alternative unit operations for the conventional gravitational clarifiers could thus be an interesting route to limit the impact of precipitates’ behavior, and, consequently, to reduce the equipment size and capital costs
[13][14][12].
3.5. Stabilility of Precipitates for Disposal
One interesting application of metal sulfide precipitation is the removal of arsenic from aqueous sources, particularly for the high content of arsenic in the As
2S
3 precipitate. This application has been studied for AMD
[31][32], industrial wastewater
[21], and acidic wastewater generated from refineries
[33][34]. Although the results obtained from these studies were promising, the stability of As
2S
3 as a residue has been recently assessed
[35][36], and there are few studies proposing methods to stabilize this residue
[33][37]. When the focus of the application of metal sulfide precipitation is the removal, supporting studies of metal/metalloids release will be required to ensure a safe disposal.
3.6. Nanoparticle Production
The use and application studies of metal sulfide nanoparticles (NPs) have increased in several fields, such as biomedicine, environmental remediation, agriculture, electronics, and catalytic reactions
[38], as well as diverse applications such as surface coating, nanoswitches, solar cell components, radiation absorbers, photocatalysts, gas sensors, and dielectric filters
[39]. Likewise, several routes for the synthesis of metal sulfide NPs have been proposed
[40], even using ionic liquids
[41]. In this context, there is an interesting opportunity to produce metal sulfide NPs directly from wastewaters or industrial solutions using a metal sulfide precipitation process. Until now, the main focus of the metal sulfide precipitation studies has been the recovery or removal of different metals/metalloids, without the possibility of enhancing the product value. A few studies have shown the promising possibility of producing NPs of CuS from AMD
[42] or PdS from aqueous media
[43], both directly using metal sulfide precipitation with biogenic sulfide as the sulfide source. Although these studies used synthetic and idealized solutions, there are several challenges remaining. For example, the optimization, control, definition of the number of stages, process integration options, and others. Future research must be developed to move forward in these interesting options.
In this aHerticle, we ein have discussed other aspects that should be taken into account in the production of NPs, such as the supersaturation control, the aggregation behavior (hydrophilicity/hydrophobicity) of precipitates, and the solid–liquid separation stage.
4. Conclusions
ThHereis study reviewn concluded the recent progress made on the metal sulfide precipitation process, including its application on several sources to recover or remove different metals and/or metalloids. This method has demonstrated a great potential to treat wastewater, efficiently recovering valuable metals or removing potentially toxic elements (metals/ metalloids) and ensuring a low content of these elements in the effluent. Furthermore, the treatment of PLS from hydrometallurgical processes is a real alternative to conventional options. Moreover, the application has expanded to Cu, Zn, Ni, Cd to Tl, As, Pd, Co, and Re. Research on this topic has also advanced in areas such as supersaturation control, new reactor types, and understanding the aggregation and colloidal behavior of precipitates. Some studies are highlighted, particularly those dealing with new materials containing a sulfide source to control the sulfide release during the reaction, and those that present the novel membrane filtration process as an alternative to conventional gravitational clarifiers for the solid–liquid separation stage. Finally, the possibility to produce metal sulfide NPs opens up an excellent opportunity to enhance the product value from the direct treatment of residue or from metallurgical plants.