2. CaO/CaCO3 TCHS
System design represents a major contribution to the application of CaO/CaCO
3 heat storage in CSP plants. The concept of calcium looping (CaL) TCHS can be traced back to the 1970s
[39][42], but most of the subsequent CaL research has focused on CO
2 capture
[40][43]. Only with the increasing demand for heat storage in recent years has the application of CaL in TCHS been extensively studied. Although the CaO/CaCO
3 heat storage technology and the CO
2 capture technology have the same chemical reaction principle
[41][44], they have remarkable differences in factors, such as reaction conditions and applications
[42][45]. When the CaL process is utilized for CO
2 capture from the flue gas of coal-fired power plants, the carbonation stage of CaO occurs in a carbonator with the flue gas containing about 15 vol% CO
2 to form CaCO
3 at the optimal temperature of 600–700 °C
[43][44][46,47]. The calcination stage of CaCO
3 occurs in a calciner at above 900 °C under a high concentration of CO
2 (>90 vol%) for CO
2 enrichment, where the required heat is provided by fuel oxygen-enriched combustion
[45][48]. When CaL heat storage is implemented in CSP stations, its carbonation and calcination conditions are more flexible. The carbonation reaction is carried out under pure CO
2 for high temperature and power generation efficiency in the exothermic stage. Gases with different concentrations of CO
2 are fed into the carbonator as required, so the exothermic temperature of 600–900 °C can be reached
[37]. Increasing the carbonation pressure can improve the limited temperature of the carbonation reaction
[46][49].
In the solar calciner, the reactants generally cannot stay for a long time, so the calcination reaction in the CaO/CaCO
3 system needs to be accomplished as soon as possible
[32]. Longer reaction time and higher temperature result in more severe sintering of CaO in the calcination stage, which is not beneficial for the carbonation of CaO
[47][50]. Thus, a shorter time and lower temperature lead to a higher carbonation of CaO due to the slight sintering
[48][49][51,52]. In addition, the solar calciner at low temperature needs fewer solar reflectors, so the cost is also reduced
[50][51][53,54]. The calcination kinetics depends not only on the calcination temperature, but also on the calcination atmosphere
[52][55]. The different calcination atmospheres for CaO/CaCO
3 heat storage were investigated, including CO
2 [52][53][55,56], steam
[54][57], and inert gases
[49][52]. For the calcination under pure CO
2 at atmospheric pressure, CaCO
3 can only be quickly decomposed at a temperature around 930–950 °C due to the limitation of thermodynamic equilibrium calculated by Equation (2)
[49][52][52,55]. If the CO
2 partial pressure is higher than the equilibrium pressure, the calcination reaction cannot occur. The utilization of superheated steam (SHS) can reduce the calcination temperature to as low as 680 °C to save energy, and the calcined CaO has strong heat storage activity
[54][57]. Nevertheless, the separation of vapor and CO
2 needs energy consumption. That is because the heat for cooling vapor is difficult to utilize. CO
2 after separation and purification is easier to use and store
[55][58]. The calcination temperature of CaCO
3 can be noticeably reduced by using inert gases, such as helium (He) or nitrogen (N
2). Compared with pure N
2, the calcination rate under pure He is faster due to the high diffusivity of CO
2 in He and the high thermal conductivity of He, and the calcination temperature is as low as 725 °C
[49][52]. However, a further issue that needs to be considered is the separation of CO
2 and He. The content related to the reaction conditions will be discussed in detail in the next section. Recently, scholars have conducted lots of research on CaO/CaCO
3 heat storage, continuously optimizing the integrated process of CaO/CaCO
3 heat storage and CSP power generation to improve efficiency
[56][57][59,60].
3. Effect of Reaction Conditions on Performance of CaO-Based Materials in CaO/CaCO3 TCHS
For the CaO/CaCO
3 TCHS system, whether the CaO-based material can maintain high carbonation performance and cyclic stability are key to heat storage. A number of studies have shown that temperature
[58][97], pressure
[59][60][98,99], atmosphere
[61][100], and particle size
[62][101] have crucial effects on the sintering rate of CaO-based materials. Therefore, it is necessary to study the reaction conditions in the stages of calcination and carbonation.
The heat storage performances of CaO-based materials are evaluated by the effective conversion
[58][97] and heat storage density
[59][98], respectively. The effective conversion denotes the ratio of the mass of CaO reacted during each carbonation cycle to the total mass of the sample before the carbonation, which is defined by Equation (3):

where
N denotes the number of TCHS cycles;
Xef, N is the effective conversion of CaO-based materials after
N TCHS cycles;
mcar, N and
mcal, N−1 denote the mass of the sample after the
Nth carbonation and the
N-1th calcination, respectively, g;
m0 represents the original mass of the sample, g;
MCaO and
MCO2 represent the molar masses of CaO and CO
2, respectively, g/mol.
Heat storage density represents the maximum heat that can be released per unit mass of CaO-based materials during each carbonation reaction, which is defined by Equation (4):
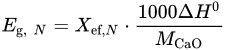
where
Eg, N is the heat storage density of CaO-based materials, kJ/kg; Δ
H0 denotes the standard reaction heat (178 kJ/mol for 0 °C; 165.5 kJ/mol for 900 °C).
4. Performance of CaO-Based Materials in CaO/CaCO3 TCHS
It has been a consensus that the effective conversion of CaO plays a decisive role in the CaO/CaCO
3 cycles heat storage. Prieto et al.
[63][112] pointed out that the inactivation of CaO was a major defect for the CSP-CaL system. As the number of CaO/CaCO
3 heat storage cycles increases, the activity of CaO decreases rapidly, and usually reaches a lower conversion over 20 cycles
[64][113]. On the one hand, the carbonation occurs rapidly under high CO
2 pressure at high temperature, so the generated CaCO
3 layer blocks pores of the unreacted CaO
[65][61]. On the other hand, due to the low Tammann temperature of calcium-based materials, CaO grains are sintered under harsh calcination conditions during multiple CaO/CaCO
3 heat storage cycles
[47][50]. The deactivation characteristics of CaO in the heat storage cycles are mainly related to the CaO precursor and the calcination/carbonation conditions. Calcium-based materials include a variety of natural ores, such as limestone, dolomite, and calcium-rich industrial waste such as carbide slag, steel slag, and fly ash
[66][114].
5. Improvement on Cyclic Thermal Storage Stability of CaO-Based Materials in CaO/CaCO3 TCHS
The heat storage performance of natural calcium-based materials, such as limestone and dolomite, declines rapidly with the number of heat storage cycles, which has an adverse effect on the CaO/CaCO
3 TCHS. The lower the performance of CaO, the higher the inert solid content of the heat storage system for transportation, preheating, and cooling, resulting in a large amount of energy loss
[67]. Studies have shown that the overall efficiency of CSP-CaL power plants increased by more than 10%, as the effective conversion of calcium-based materials increased from 0.07 to 0.5
[68][63]. Thus, it is beneficial to improve the cyclic heat storage performance of calcium-based materials and prepare calcium-based heat storage materials with high efficiency and stable performance, which have become the focus of attention of researchers. Adding a dopant with a high Tammann temperature to calcium-based materials is one of the most common methods to slow down the sintering of CaO-based materials. The supporter dispersed between the CaO grains plays a supporting role, which prevents the agglomeration of the CaO grains at high temperatures to a certain extent and enhances the sintering resistance of the CaO-based material
[69][123].
6. Improvement on Optical and Thermal Properties of CaO-Based Materials in CaO/CaCO3 TCHS
The Tammann temperature of calcium-based materials is relatively low, so CaO grains agglomerate and grow up during cyclic heat storage process at high temperature, leading to the blockage of the pore structure, which is manifested as a gradual decline in heat storage performance
[40][69][43,123]. A large number of researches have focused on slowing down the sintering speed of calcium-based heat storage materials to improve cyclic stability. The volumetric heat collection is more suitable for CaO/CaCO
3 heat storage system, which requires calcium-based materials with great optical and thermal properties. However, natural calcium-based materials usually have poor optical absorption capacities and thermal conductivity. In recent years, the optical absorption capacity and thermal conductivity of natural calcium-based materials have been given more attention and represent a valuable research direction.
Han et al.
[70][142] prepared composite materials by impregnating in H
3BO
3 solution with CaCO
3 and adding expanded graphite with high thermal conductivity for heat storage. They found that the thermal conductivity of the composite materials increased by 60% when 3 wt% expanded graphite was added. The expanded graphite exhibited strong sintering resistance. The heat storage density of the composite material was 1313 kJ/kg after 50 cycles, while that of limestone was only 452 kJ/kg. On this basis, Han et al.
[71][143] also studied an effective compression method to make graphite nanosheets better support the pore structure of CaO-based materials, so the obtained composites possessed a higher volumetric energy density. However, it is worth noting that CO
2 attaches to graphite at high temperatures to form CO gas. More consideration should be given when choosing graphite as an additive. Da et al.
[72][79] put forward a new idea to increase the blackness of calcium-based materials to achieve the direct absorption of solar energy in a CaO/CaCO
3 heat storage system. Their experiments showed that adding black FeMnO
3 and Fe
2O
3 to CaO by the sol-gel method improved the optical absorption properties of the materials. When the molar ratio of Ca/Mn/Fe was 100:4:8, the solar absorption of the composite reached 89.81% as exhibited in
Figure 2. In addition, the existence of FeMnO
3 and Fe
2O
3 also enhanced the sintering resistance of CaO. The effective conversion of Ca/Fe/Mn composites remained as high as 0.8 after 20 cycles.
Figure 2. Optical absorption properties of CaO-based composites [72]: ( Optical absorption properties of CaO-based composites [79]: ( a
) Spectrum; (
b
) Absorption.
Moreover, Teng et al.
[73][82] optimized the structure of the Ca/Fe/Mn composite by using calcium gluconate as the precursor to prepare a porous Ca/Fe/Mn composite with an optical absorption rate of 90%. The heat storage capacity of the Ca/Fe/Mn composite decreased by 3.31% in 60 cycles. The average heat storage density of the composite after 60 cycles was 1450 kJ/kg, which was 1.76 times as high as that of CaCO
3, indicating that it had higher cyclic stability. Song et al.
[74][144] used aluminum nitrate and iron nitrate as precursors to dope iron and aluminum into CaCO
3 powder by the sol-gel method. They found that the decomposition rate of the composite increased and the decomposition temperature decreased. After 50 cycles, the heat storage density of the composite only dropped by 4.5%, which was about 87% higher than that of pure CaCO
3. Similarly, the average optical absorption rate of the composite achieved 45.6%, while that of pure CaCO
3 reached only 8%. Li et al.
[75][145] used Ca(OH)
2 powder, MnC
4H
6O
4·4H
2O and SiC by extrusion-spheronization method to prepare Mn/SiC doped CaO pellets. They found that when SiC and MnO
2 were both doped at 5 wt%, CaO pellets exhibited the highest the optical absorption and heat storage capacity. In addition, the effective conversion of the Mn/SiC doped CaO pellets remained 0.48 after 30 cycles, while that of the pure CaO pellets achieved only 0.34. Similarly, the average optical absorption of the Mn/SiC doped CaO pellets reached 53%, while that of the original CaO particles was only 3%. Yang et al.
[76][146] prepared Ca/Fe/Mn composite heat storage materials by utilizing carbonaceous microspheres as templates, which mainly consisted of CaCO
3 and Ca
2FeMnO
5. The average spectral absorption rate of the synthetic material with the molar ratio of Ca/Fe/Mn = 100:2:7 reached 76.8%, while that of pure CaCO
3 was only 10.8%. Zheng et al.
[77][147] examined a variety of dark composite calcium-based heat storage materials by the sol-gel method, including Ca/Cu, Ca/Cu/Fe, Ca/Cu/Co, Ca/Cu/Cr, Ca/Cu/Mn, and Ca/Al/Cu/Fe materials. The results showed that Ca/Cu/Co, Ca/Cu/Cr, and Ca/Cu/Mn materials had strong optical absorption capacities, and their average spectral absorption of solar energy was greater than 60%.
Table 2 summarizes the heat storage properties of the different CaO-based materials reported in the literature. It is found that adding dopants is still the most effective and common method to improve the heat storage stability of CaO-based materials. However, it is still unavoidable that the activity of CaO-based material decreases during long-term heat storage cycles. Calcium-based materials often need to add enough supporters to maintain relatively stable heat storage performance. This also decreases the content of CaO in the calcium-based material, resulting in a decrease in the heat storage density of the material per unit mass. Thus, how to enhance the heat storage performance and cyclic stability of calcium-based materials remain important. In addition, how to improve the optical and thermal properties of CaO-based materials is also the focus of researchers.
Table 2. Comparison of heat storage properties of CaO-based materials reported in the literature.
| Additives |
|
| Doping Ratio (wt%) |
|
| Carbonation Pressure (bar) |
|
| Cycles |
|
| Effective Conversion |
|
| Reference |
|
| SiO2 |
|
| 10% |
|
| 1 |
|
| 20 |
|
| 0.30 |
|
[78]
|
[126]
|
| SiO2 |
|
| 30% |
|
| 1 |
|
| 20 |
|
| 0.34 |
|
[78]
|
[126]
|
| SiO2 |
|
| 5% |
|
| 1 |
|
| 20 |
|
| 0.20 |
|
[79]
|
[127]
|
| SiO2 |
|
| 37.5% |
|
| 1 |
|
| 45 |
|
| 0.20 |
|
[80]
|
[129]
|
| SiO2 |
|
| 20% |
|
| 5 |
|
| 50 |
|
| 0.29 |
|
[81]
|
[130]
|
| Al2O3 |
|
| 20% |
|
| 5 |
|
| 50 |
|
| 0.62 |
|
[81]
|
[130]
|
| Al2O3 |
|
| 5% |
|
| 1 |
|
| 20 |
|
| 0.55 |
|
[82]
|
[131]
|
| ZrO2 |
|
| 5% |
|
| 1 |
|
| 10 |
|
| 0.22 |
|
[83]
|
[109]
|
| ZrO2 |
|
| 20% |
|
| 5 |
|
| 50 |
|
| 0.67 |
|
[81]
|
[130]
|
| ZrO2 |
|
| 40% |
|
| 5 |
|
| 50 |
|
| 0.45 |
|
[81]
|
[130]
|
| ZnO |
|
| 20% |
|
| 5 |
|
| 50 |
|
| 0.07 |
|
[81]
|
[130]
|
| Fe2O3 |
|
| 20% |
|
| 5 |
|
| 50 |
|
| 0.08 |
|
[81]
|
[130]
|
| Ni |
|
| 20% |
|
| 5 |
|
| 50 |
|
| 0.14 |
|
[81]
|
[130]
|
| BaCO3 |
|
| 9.5% |
|
| 5 |
|
| 50 |
|
| 0.09 |
|
[81]
|
[130]
|
| Li2SO4 |
|
| 5% |
|
| 1 |
|
| 11 |
|
| 0.48 |
|
[84]
|
[137]
|
| Al2O3/CeO2 |
|
| 5%/5% |
|
| 13 |
|
| 30 |
|
| 0.79 |
|
[85]
|
[136]
|
| Graphite |
|
| 20% |
|
| 5 |
|
| 50 |
|
| 0.25 |
|
[81]
|
[130]
|
| H3BO3/Graphite |
|
| 3% |
|
| 1 |
|
| 50 |
|
| 0.41 |
|
[70]
|
[142]
|
| Mn/Fe |
|
| - |
|
| 1 |
|
| 20 |
|
| 0.80 |
|
[72]
|
[79]
|
| Al/Citric acid |
|
| - |
|
| 1 |
|
| 20 |
|
| 0.7 |
|
[86]
|
[133]
|
| Acetic acid(Ac) |
|
| - |
|
| 1 |
|
| 30 |
|
| 0.56 |
|
[87]
|
[140]
|
| Mg/Ac |
|
| - |
|
| 1 |
|
| 30 |
|
| 0.70 |
|
[87]
|
[140]
|
| NaY |
|
| 20% |
|
| 5 |
|
| 50 |
|
| 0.23 |
|
[81]
|
[130]
|
| HY |
|
| 20% |
|
| 5 |
|
| 50 |
|
| 0.16 |
|
[81]
|
[130]
|
| Mor |
|
| 20% |
|
| 5 |
|
| 50 |
|
| 0.15 |
|
[81]
|
[130]
|