Bone defects characterized by limited regenerative properties are considered a priority in surgical practice, as they are associated with reduced quality of life and high costs. In bone tissue engineering, different types of scaffolds are used. These implants represent structures with well-established properties that play an important role as delivery vectors or cellular systems for cells, growth factors, bioactive molecules, chemical compounds, and drugs. The scaffold must provide a microenvironment with increased regenerative potential at the damage site. Magnetic nanoparticles are linked to an intrinsic magnetic field, and when they are incorporated into biomimetic scaffold structures, they can sustain osteoconduction, osteoinduction, and angiogenesis.
1. Introduction
Bone tissue engineering (BTE) is an important topic in orthopedic
[1] and craniofacial surgery
[2][3]. To restore defects due to prosthetic implants and degenerative diseases such as osteoarthritis, osteoporosis, Paget’s disease, or osteogenesis imperfecta, biomimetic scaffolds can be involved
[4][5][6][7][8]. Bone reconstruction is a complex process starting from inflammation, regeneration, and remodeling, each with its unique physical and biological mechanisms. Within this process, an important aspect is the action of the stem cells combined with growth factors or cytokines. Mesenchymal stem cells (MSCs) usually differentiate into osteoblasts, and hematopoietic stem cells (HSCs) are directly linked to osteoclast formation
[9]. These two types of cells are essential for the formation and remodeling process of new bone. In the case of small bone defects, the healing phenomenon is spontaneous, but some supplementary interventions are required in the case of large defects
[10][11][12]. Schemitsch
[13] proposed a classification of bone defects. He considered that small defects are characterized by 50% cortical circumference loss and a defect size of less than 2 cm, intermediate defects consist of a cortical circumference loss higher than 50% and a defect size between 2 and 6 cm, and large defects exhibit a size greater than 6 cm
[14]. Autografts or allografts are harvested using an invasive procedure associated with high risk of infection or disease transmission; even graft rejection can occur
[15][16]. Usually, bone from the iliac crest, autologous vascularized fibular graft, or allograft is used. Another classical solution consists of the use of bone transport fixators; however, this method is linked to an increased healing time and pain. Autografts represent the gold standard in orthopedy, but this method is not always safe due to donor site morbidity effects and limited availability
[17][18]. Regarding allografts, immunogenic responses or vascularization graft absence should be taken into account
[19]. Grafting techniques are expensive, and due to high graft demand on the worldwide market, problems in bone defect treatments are foreseen
[20][21][22][23].
1.1. Scaffolds for Bone Tissue Engineering
Bone scaffolds can be defined as artificial platforms dedicated to supporting and repairing a defect. A scaffold is necessary when an organ or a tissue is damaged, and in these cases, a three-dimensional (3D) structure is indicated. The most important properties and design features for a scaffold are biocompatibility, mechanical properties, biodegradability, pore size and interconnectivity, osteoinductivity, porosity, stability, antimicrobial effects, osteoconductivity, osteointegration, and osteogenesis, as depicted in
Figure 1 [24][25][26][27].
Figure 1. The most important attributes of a scaffold.
For 3D scaffolds, a few criteria must be met before qualifying as an ideal implant. First, the scaffolds should have sufficient porosity to allow for tissue growth, adequate signaling, cellular ingress, and vascularization
[28][29][30]. However, it is important to note that the mechanical properties of scaffolds are inversely proportional to their porosity. Therefore, recent studies
[31][32] have recommended that scaffolds with a porosity of 200–350 μm are suitable for bone tissue regeneration. In the case of small bone defects, two-dimensional structures can be used as scaffolds to facilitate better interaction between cells and implant biomaterials
[33].
After the scaffold is implanted, it is expected to provide a structure that is beneficial for cell proliferation, adhesion, and differentiation to create an adequate biomechanical medium for tissue regeneration, permit the dissemination of oxygen and nutritional substances, and to allow for the encapsulation of cells that will be released and combined with growth factors
[34][35]. Scaffolds can be very useful for delivery of drugs and cells and, in the case of organ disease or failure, can sometimes be used to restore normal functionality. In bone tissue engineering, it is well known that bone-like porous structures ensure blood circulation, nutrient movement, and a combination of osteogenic cells and bioactive substances, which promote mineralization and angiogenesis in the transplanted graft. Chemical composition and topological aspects strongly influence scaffold surface properties, which are essential in cell adhesion and proliferation. The implant surface is the main boundary between biomaterial and tissue
[36][37][38]. Surface roughness is considered a critical factor in osteoblasts’ adhesion and differentiation, and the mechanical properties of the scaffold must be similar to those of human bone to ensure successful and healthy bone grafting
[39][40]. The implant must support the bone ingrowth process until the new bone can sustain itself. The efficacity of the regenerative process plays an important role through pore distribution, exposed surface area, the material’s porosity, the rate of cell penetration within the scaffold volume, and the extracellular matrix (ECM) architecture
[41].
1.2. Biomaterials Used for Bone Tissue Engineering
Research has been focused on different types of scaffolds that show biological components
[42][43]. These implants are, unfortunately, expensive, so scaffolds that do not contain so-called “biologics” provide significant advantages. They are adequately manufactured to collect and recruit cells from the tissue placed in the scaffold vicinity to enhance new bone formation. The use of adequate bioactive agents can sometimes be helpful for recruitment of cells with osteogenic characteristics
[42][44]. As a result, the of mineralized matrices occurs in the entire implant structure
[45][46]. A high amount improves the regenerative process. Angiogenesis is another essential aspect that sustains the needs of the new tissue
[47].
Bioactive materials such as bioglass and calcium-phosphate-based ceramics are usually used in bone tissue engineering. They interact with natural tissue through an ion-exchange reaction, which leads to the formation of an active apatite layer on the scaffold
[48][49]. Hydroxyapatite and tricalcium phosphate are biodegradable and begin to dissolve when introduced into human or animal bodies. Due to an increased similarity with human bone, scaffolds can be manufactured from bioactive ceramics that are corrosion-resistant, osteoconductive, and biocompatible
[42]. Their main disadvantage is related to the fact that they are brittle and porous, and an increased risk of fracture can be foreseen. The most commonly used ceramics in BTE are hydroxyapatite, calcium phosphates, and β—tricalcium phosphate.
Another important class of materials is bioactive glasses. They have a composition based on SiO
2, P
2O
5, and B
2O
3. The silanol groups result from SiO
2 dissolution and precipitate into a silica layer that sustains the migration of phosphate and calcium ions, leading to the appearance of a layer of calcium phosphate
[50][51]. In some bioactive glasses, partial replacement of SiO
2 with B
2O
3 generates borosilicate or borate glasses that exhibit a controllable biodegradation rate. A faster degradation rate of the scaffold was noticed in the case of phosphate glasses that include Na
2O and CaO. The advantages of bioactive glasses are controlled resorbability and osteoconduction. The main drawbacks are that the mechanical properties of the glass have values that differ from those of human bone and that the material must be tuned to control its degradation rate and ion release to avoid toxicity. Another disadvantage of bioactive glass was observed when 3D porous scaffolds were made; a crystallization phenomenon was identified during the sintering step
[52]. As a result, the reduced compressive strength of the implant was put in evidence, which makes these types of materials suitable for scaffolds dedicated to use in low-load defect locations or as part of a composite structure with polymers or bioactive ceramics
[53].
One of the most used materials in scaffold manufacturing is polymers, which can have natural or synthetic origins. The main polymeric implant properties are divided into three categories based on processing conditions, their intrinsic nature, and the final product. The intrinsic properties, such as density, solubility, crystallinity, transition temperature, mechanical properties, transparency, electromagnetic behavior, etc., depend on chemical composition and structure
[54][55]. The viscosity, the melt strength, and melt flow index are considered the main processing characteristics and put in evidence the material behavior during the production process. The product’s properties combine those mentioned above and include esthetic properties, environmental behavior, and degradation conditions
[56]. Polymeric scaffold biodegradability is very important and is defined as a gradual breakdown process of the material. There are two main biodegradable polymers: stepwise polycondensation and ring-opening polymerization materials. The first group includes polysaccharides and proteins
[57], and the second contains aliphatic and aromatic polyesters. Most natural polymers are degraded by different enzymes. Polysaccharide-based biomaterials are degraded by amylases and lysosomes inside the human body. Many synthetic polymers are degraded by a hydrolytic process. The most common non-biological degradation processes are hydrolysis and erosion. The mechanical properties of polymers are influenced by molecular weight and crystallinity grade, which are directly linked to the degradation process of the material
[58][59][60]. To obtain a successful treatment in the case of biodegradable polymers, it is important to maintain adequate mechanical strength to reconstruct load-bearing tissues such as bone. Rheological parameters such as Young’s modulus, flexural modulus, maximum strain, and tensile/compressive strength are always measured when a new implant enters the market
[61]. The advantages of synthetic polymeric implants are that they can be manufactured under controlled conditions, and as a direct consequence, their degradation rate, mechanical properties, and porosity can be modified in accordance with different medical applications
[62][63]. They can be produced in large quantities and can exhibit a homogenous structure. Better interaction with cells characterizes natural polymers, but they are found in limited quantity
[64]. Their main drawback is that their properties cannot be controlled, as in the case of synthetic polymers, their toxicity must be carefully addressed
[65].
Magnetic nanoparticles (MNPs) can be incorporated into scaffolds manipulated in situ under electromagnetic forces
[66][67][68]. Due to the influence of magnetic field, these implants offer the possibility of increased osteogenesis and angiogenesis at large bone defect sites
[69]. Many literature studies have proven that scaffolds reinforced with MNPs support the differentiation and proliferation of osteoblasts in the presence and absence of a magnetic field by activating dedicated signal pathways
[44][70][71][72][73][74][75]. Treatment of bone tumors with methods such as magnetic hyperthermia or photothermal therapy is also possible.
The main magnetic scaffold components are presented in
Figure 2 [76][77], taking into account the scaffold geometry and shape and its combination with stem cells
[78][79], growth factors or bioactive molecules
[80], chemical compounds, and drugs
[81].
Figure 2. Main components of a magnetic scaffold used in BTE.
2. Biomaterials Used in Magnetic Polymeric Scaffolds Designed for Bone Regeneration
Biomaterials for scaffolds must possess the ability to present biomimicry by taking into account the properties mentioned above. Many studies have been conducted to determine the best material combinations to obtain an enhanced osteogenic and angiogenic effect of the scaffold when implanted in the human body
[2][42][69][82][83]. In this direction, magnetic nanoparticles can be successfully combined with polymer scaffolds, obtaining an increased osteogenic effect on the stem cells
[44][70][71][72][73][75]. Through MNPs, drugs or bioactive agents can be directly guided to the defect site to help in bone regeneration
[84].
Figure 3 shows several types of biomaterials and scaffolds used in bone tissue engineering.
Figure 3. Types of biomaterials and scaffolds used in BTE.
2.1. Magnetic Scaffold Manufacturing Technique
The scaffold manufacturing technique is chosen according to the following criteria. The chemical properties of the material must not be modified during the production process to negatively influence the implant’s clinical use or alter its biocompatibility
[85]. There are two types of manufacturing technologies: conventional and the advanced techniques. Conventional techniques are based on subtractive routes that consist of material removal from an initial bulk volume to obtain the desired shape of the implant. The main drawback is that a random architecture of the scaffolds results
[85]. These technologies imply the use of organic solvents, which may harm cell functions and viability
[86].
On the other hand, advanced methods permit the control of scaffold geometry and pore size. Tunable mechanical properties characterize the implants, in accordance with the surrounding tissue attributes. These methods allow for compositional variation of different materials across the interface, surface, or volume of the scaffolds. In addition, they do not use toxic organic solvents, which is directly linked to increased scaffold biocompatibility
[87].
Some of the most important techniques for the manufacture of polymeric scaffolds using conventional technologies are freeze drying, electrospinning, gas foaming, solvent-casting particulate leaching, and thermally induced phase separation.
Freeze drying is based on polymeric slurry production. After that, it is poured into a mold and frozen. The resulting ice crystals generate the scaffold pores, and lyophilization occurs once the slurry undergoes solidification. Scaffolds manufactured through freeze-drying exhibit a porous structure with low stiffness and small pores. The main disadvantages of this method are high energy consumption, the use of cytotoxic solvents, and the long duration of the procedure
[87][88][89]. The electrospinning technique consists of an electric charge liquid jet used to generate, with the help of a syringe pump, fine polymeric fibers, creating a collector on a nanofibrous architecture. The system’s main components are a high-voltage power supply, a syringe pump, a spinner with a metallic needle, and a collector connected directly to the ground. The electric field strength overcomes the surface tension of the material droplet, and a charged liquid jet, which is continuously deformed by the electrostatic repulsion phenomenon, is deposited on the collector. Fibrous polymeric scaffolds are manufactured using this technology
[90]. A drawback of this method is that it is linked to organic solvent use. Sponge-like scaffolds based on inert gases that pressurize molded polymers with fluoroform and water are obtained using gas foaming. The material becomes saturated and is characterized by gas bubbles. An advantage of this technique is the avoidance of toxic solvents, and the disadvantages are the heat developed during the compression molding process, isolated pores, and a continuous skin layer
[91]. Solvent-casting particulate leaching requires a solvent containing a dissolved polymer solution to be mixed with specific diameter-sized salt particles. By evaporating the solvent, an embedded salt matrix is obtained. Using water, the salt leaches out, generating a highly porous structure. The advantages of this method are high porosity and a controllable pore diameter through salt particle size. The main drawbacks include residual solvent presence and scaffolds with a simple geometry
[92][93]. In the case of the thermally induced phase separation method, the polymer solution is subjected to a low temperature, so a liquid–liquid phase separation is obtained. Two phases result: a polymer-rich phase and a polymer-poor phase. The polymer-poor phase is eliminated during solidification. A highly porous nanoscale structure is obtained
[94].
The advanced methods are part of the class of rapid prototyping technologies that include selective laser sintering (SLS), selective laser melting (SLM), stereolithography (SL), fused deposition modeling (FDM), and binder jetting (BJ).
SLM and SLS are derived from the powder bed fusion class and can be used to obtain scaffolds with desired shape architecture and controlled porosity; however, small details such as sharp corners or complicated boundaries cannot be designed
[95]. Through SLS, powder particles are bonded in thin layers under a high-power laser effect. The last formed layer is bounded to the previous layer as indicated in a predefined computer-aided design (CAD) file. The main drawbacks of this technology are the high operating temperature and the fact that residual powder must be removed
[96][97][98]. SL includes a tank with a photosensitive liquid polymer placed in a thin layer on a movable built platform. The desired geometry layer is defined using an ultraviolet (UV) laser, the platform is lowered, and the process is repeated. This method is fast and provides a high resolution. Its drawbacks are brittleness and low mechanical strength of the scaffold
[95]. FDM implies a molten thermoplastic material extruded through a nozzle to form a continuous thin filament printed on an imposed CAD pathway in a layer-by-layer procedure. Through this technique, a controlled porosity can be obtained
[99]. The method does not require toxic solvents
[100][101][102]. BJ technology is based on a deposited powder bed on which, using a printing head, a liquid binder solution that describes the required geometry is placed. The advantages of this method are the manufacture of scaffolds adapted to the patient’s anatomy or multilayered implants used for hybrid tissue regeneration. The unbounded powder removal, the limited pore size configuration, and the possibility of the binder being dissolved are the main drawbacks
[2]. Three-dimensional bioprinting technology offers the possibility of including cells and differentiation or growth factors in the scaffold geometry. Its main drawback is that during the post-fabrication stages, the solvent must be entirely removed
[103][104].
Figure 4 shows some of the conventional and advanced preparation methods and examples of obtained polymeric scaffolds.
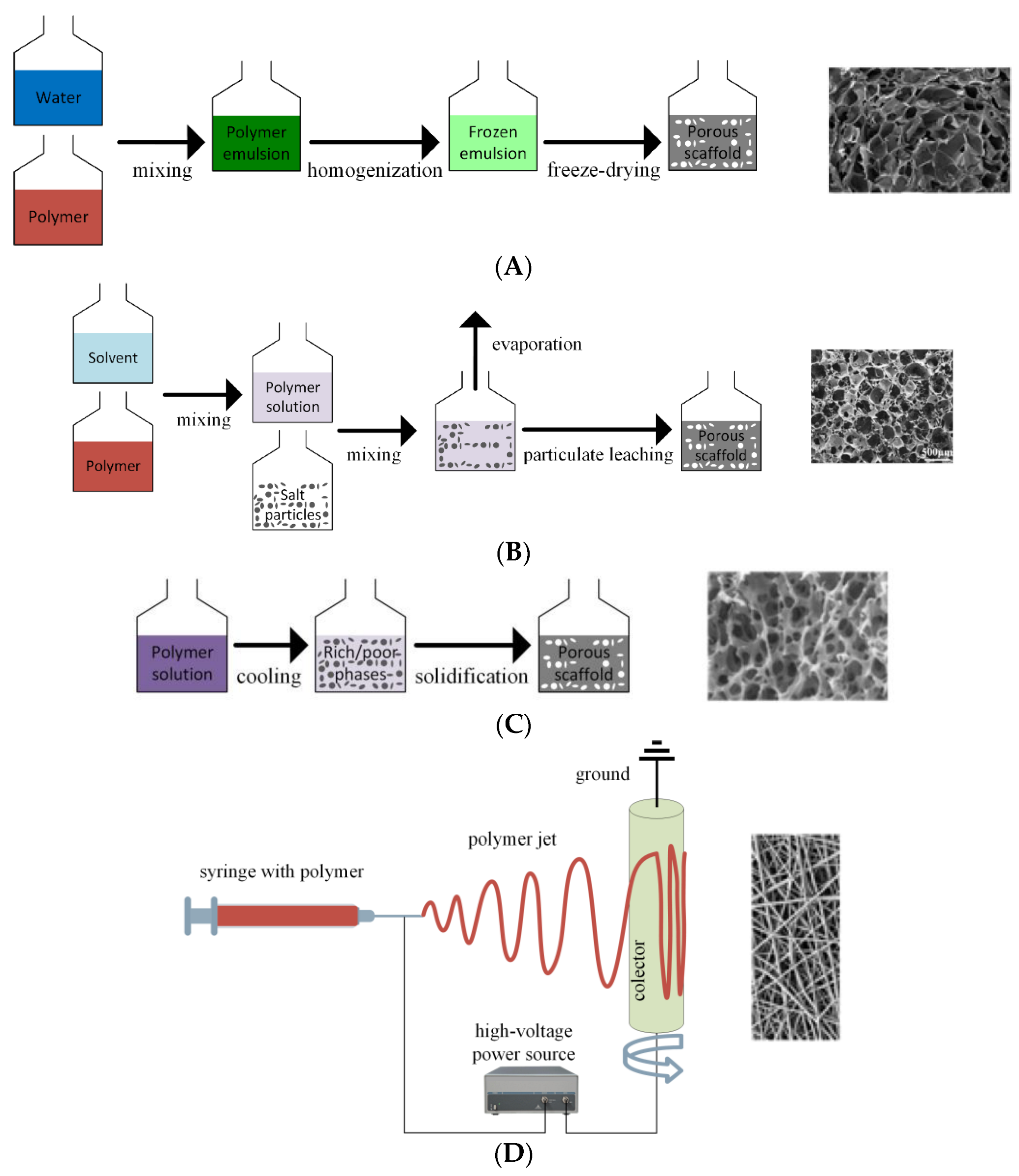
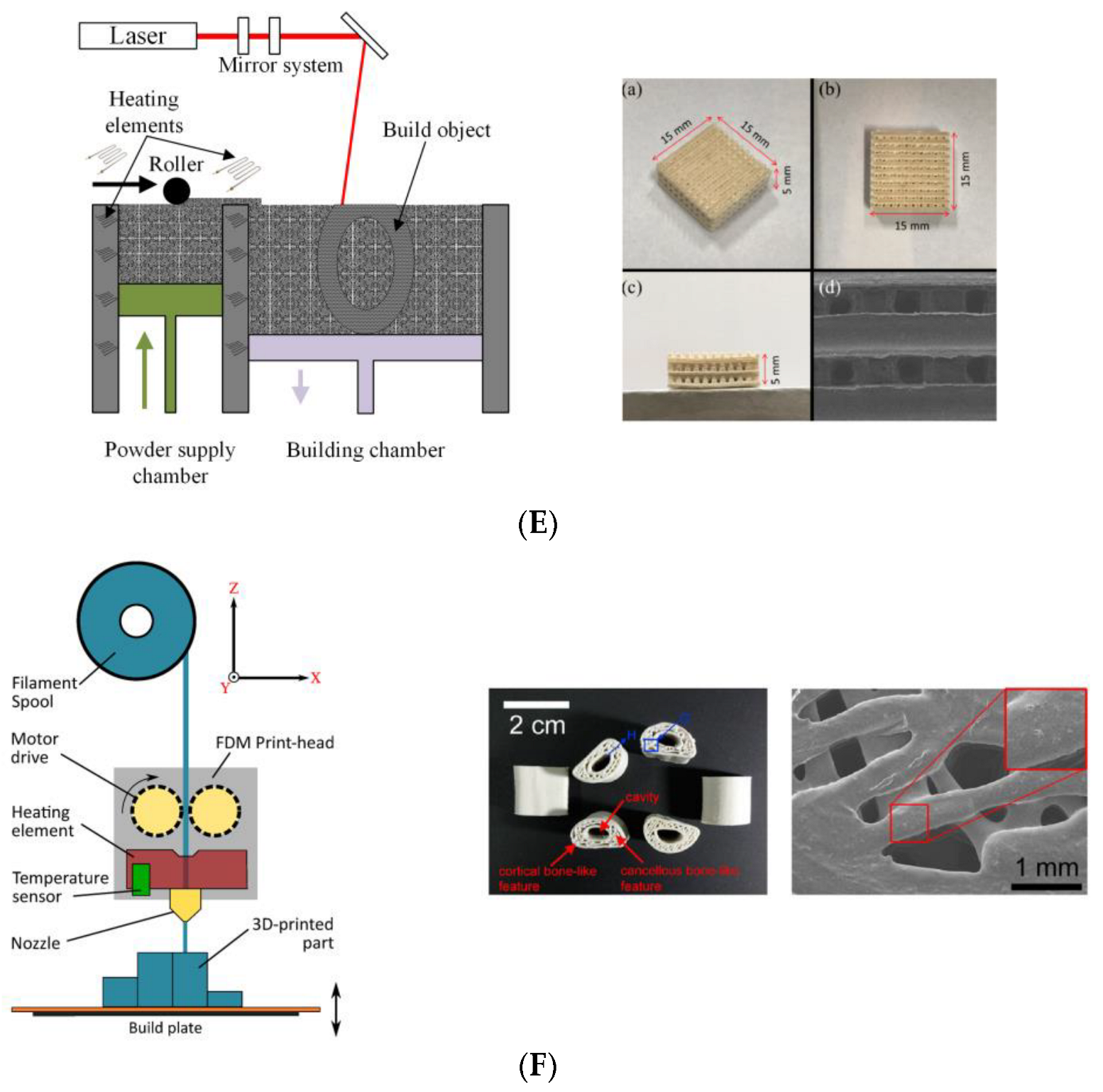
Figure 4. Examples of conventional and advanced preparation methods for polymeric scaffolds: (
A) freeze drying; (
B) solvent-casting particulate leaching; (
C) thermally induced phase separation; (
D) electrospinning; (
E) selective laser sintering ((
a–
c) optical images and (
d) SEM image); ((
A–
D) (
right), and (
E) are licensed under CC-BY 4.0).
As previously mentioned, MNPs can be inserted into polymeric scaffolds to enhance cell adhesion and differentiation or to apply regenerative or oncological treatments. They are fabricated using solvothermal, hydrothermal, coprecipitation, sol–gel, electrochemical, and laser pyrolysis methods
[77]. Other preparation technologies reported in the literature are powder metallurgy, evaporation synthesis, laser ablation, and microbial methods
[105]. The most used technology is precipitation from a solution. Magnetite (Fe
3O
4) is prepared based on an aqueous solution of Fe
3+ and Fe
2+ chloride combined with a base. Coprecipitation consists of a ferric and ferrous hydroxide suspension that is oxidized through different chemical substances (i.e., Fe
2+ salt, nitrate ions, and a base) or a mixture of stoichiometric ferric and ferrous hydroxides that are aged in aqueous media. Other important methods are based on microemulsions, which generate nanoparticles with tunable sizes and distributions, reverse micelle solutions, or polyols, as explained in detail in
[77].
Different methods have been reported in the literature to obtain magnetic scaffolds. Lu et al.
[106] added SrFe
12O
19 nanoparticles prepared by the molten salt method and MBG microspheres in CS solution. After a stirring procedure, the samples were frozen under an external magnetic field, and finally, a freeze-drying step was applied. Cojocaru et al.
[107] made magnetic scaffolds from natural biopolymers combined with Fe
3O
4 MNPs using a biomimetic coprecipitation method. Before this process, different concentrations of MNPs were added to the polymer solution, and after that, freeze-drying technology finished the production method. Samal et al.
[108] designed silk scaffolds based on a salt-leaching procedure in which they infused MNPs under a static magnetic field effect generated by a permanent magnet. Dankova et al.
[109] made a mixture of polycaprolactone, adding MNPs based on the dispersion method. Then, fibrous scaffolds were generated through the electrospinning method. De Santis et al.
[110] designed, through rapid prototyping, 3D fully biodegradable magnetic scaffolds made from polycaprolactone reinforced with iron-doped hydroxyapatite (FeHAp) nanoparticles processed through a 3D fiber deposition method. They investigated the influence of FeHAp nanoparticle concentration to adapt the implants to dedicated medical applications such as advanced bone tissue engineering or magnetic hyperthermia.
The choice of the scaffold production method must consider the geometry of the required implant (because it should be patient-oriented), the toxicity grade of the MNPs, and its cost. Magnetic scaffolds represent an innovative approach for large bone treatments, and they are applicable for drug delivery, cell guidance based on magnetic force action, and cancer therapy.
2.2. Magnetic Nanoparticles Used for Scaffold Loading
Magnetic nanoparticles exhibit unique material properties because they can be manipulated using an externally applied magnetic field. These nanomaterials are made from a magnetic core, which contains a different oxide of ferromagnetic metals such as iron (Fe), cobalt (Co), or nickel (Ni) that can be coated with a biocompatible material with unique properties for medical applications
[77][111][112].
Figure 5a shows a classic scheme of a coated MNP that can be used for ligand transport, responsive elements, and fluorophores.
Figure 5b,c show scanning electron microscopy (SEM) images and elemental analyses of Fe
3O
4 uncoated MNPs functionalized with chitosan.
Figure 5. Representation of an MNP, SEM images, and elemental analysis of Fe
3O
4 nanoparticles prepared through coprecipitation method: (
a) classic illustration of MNP structure; (
b) SEM images and elemental analyses of uncoated MNPs; (
c) SEM images and elemental analyses of MNPs functionalized with chitosan.
The most common applications of MNPs are magnetic hyperthermia, magnetic drug targeting therapy, and as magnetic resonance imaging (MRI) contrast agents. The size of the magnetic particle represents the main parameter that separates ferromagnetic and superparamagnetic behavior. Below a critical diameter, the MNPs present a so-called superparamagnetic state characterized by a magnetic single-domain configuration with a sigmoidally shaped magnetization curve. High magnetic susceptibility and saturation magnetization values characterize superparamagnetic iron oxide nanoparticles (SPIONs). These nanoparticles are special MNPs extensively used in biomedicine
[113][114]. They are biocompatible and chemically stable and exhibit environmentally friendly behavior. Superparamagnetic behavior is directly linked to the magnetic anisotropy of the MNPs measured along the easy magnetization axis of the particle, which is a direction characterized by a minimal value of magnetic anisotropy energy. In the case of spherical magnetic nanoparticles, the total magnetic anisotropy can be considered a barrier in the magnetization direction change
[115]. At very low values of the particle diameter, the anisotropy energy is almost equal to the heat activation energy
[116], and when the latter is increased, there is no preferential direction for the magnetic moment orientation. The behavior of SPIONs could be assimilated to that of paramagnetic atoms
[117][118]. The value of the temperature at which the thermal activation is higher than the magnetic anisotropy energy is denoted in the literature as the blocking temperature
[119][120].
It was previously shown that particles with a large diameter are more toxic than smaller particles when an alternating low-frequency magnetic field is applied
[121]. At a diameter lower than 200 nm, the nanoparticles are not trapped in the sanguine system and are expelled through the mononuclear phagocyte system and hepatic filtration function
[122][123].
The material surface must be modified to improve the drawbacks of magnetic nanoparticles, such as poor biodegradability, chemical instability, and moderate biocompatibility. One of the most used methods is MNP functionalization with different materials. Biofunctional molecules such as ligands, antibodies, or receptors can link different nanostructures of the human body to the magnetic core, making some treatments more efficient
[124]. Another technology consists of the integration of SPIONs or, in general, MNPs with other metallic nanoparticles, which leads to so-called heterodimer structures. These unique materials permit the attachment of functional molecules to a specific surface part of the heterodimer that can bind to different receptors or act as agents in imaging techniques
[125]. A direct application is a platform for bacterial detection
[126][127].
The chemical stability and solubility of MNPs must be carefully controlled in biological media. It is well known that by incorporating MNPs into biodegradable polymeric scaffolds, owing to their hydrophilic nature, the implant wettability is improved, and increased cell adhesion and proliferation are observed
[128]. The MNP concentration also plays an important role in the improvement of mechanical properties. Some studies have evidenced well-established MNP concentrations beyond which a decrease in mechanical strength is reported
[129][130]. However, as an overall finding, the addition of MNPs can be linked to a reduction in the porosity percentage of PCL scaffolds and an increase in the porosity grade of chitosan or collagen implants
[131][132]. When SPIONs are incorporated into polymeric scaffolds, because each particle is a single magnetic domain, the implant exerts a magnetic influence on the receptors placed on the cell membrane, activating the intracellular signaling pathways
[130][133]. Due to the presence of magnetic induction, the cell cycle is accelerated, and osteogenic differentiation is put in evidence
[109].
Modern magnetic scaffolds consist of a matrix made from different materials and magnetic nanoparticles chemically doped or physically loaded into the implant structure. The matrix is usually made from bioceramics, polymers, or hydrogels, and it is a suitable tool in regenerative medicine and anticancer therapy because the magnetic hyperthermia effect can be combined with the osteoinductive properties of the MNPs
[134].
2.3. Biopolymers for Magnetic Scaffolds
Biodegradable polymers can be used to manufacture the scaffold matrix in BTE. In the case of medical applications, increased attention is devoted to the cellular environment and the interaction between materials and cells
[135][136]. Due to their specific properties, such as biodegradability, high porosity, important surface-to-volume ratio, and favorable mechanical properties, polymeric scaffolds have become among the most used implants for BTE
[137][138].
2.3.1. Natural Biopolymers
As a function of structure and monomeric units, there are three important polymer types: polysaccharide-based (e.g., chitosan, chitin, hyaluronic acid, and alginate), polypeptide- and protein-based (e.g., collagen, silk, and gelatin), and polynucleotide-based
[25] polymers.
Members of the polysaccharide-based group are made from disaccharide or monosaccharide chains. Chitin and chitosan are characterized by non-toxicity, biocompatibility, and biodegradability properties
[139]. They owe reactive species as hydroxy and amino groups, high charge density and exhibit broad hydrogen-bonding capabilities and a single chemical structure. Due to their reactive species, chitosan and chitin can be easily linked to different biomolecules to increase the biocompatibility of scaffolds. The biodegradation rate of these biopolymers depends on the acetyl content, and their
in vivo breakdown occurs as a result of lysozymes. If chitosan is modified in an appropriate manner, scaffolds for bone regeneration can be produced
[140]. Zhao et al.
[131] prepared magnetic bioinspired micro/nanostructured composite scaffolds based on a chitosan/collagen organic matrix. They incorporated nanohydroxyapatite (nHAp) and Fe
3O
4 nanoparticles into scaffolds. The matrices were prepared by in situ crystallization and freeze-drying technique.
In vitro analyses including physicochemical and biocompatibility tests proved that [CS/Col]/[Fe
3O
4/nHAp] magnetic implants were characterized by good structural and mechanical properties and were beneficial for cell adhesion and proliferation. Enhanced osteogenic differentiation due to the presence of MNPs was also noticed. Mineralization tests showed that the magnetic scaffolds have a very good in situ biomimetic mineralization process. Lu et al.
[106] fabricated magnetic nanoparticles of SrFe
12O
19 that were incorporated in modified MBG/CS porous scaffolds. These implants proved to have beneficial properties against tumors with excellent bone regeneration effects. SrFe
12O
19 nanoparticles had an improved photothermal conversion property. Cojocaru et al.
[104][107] made biopolymer–calcium phosphate composites with the inclusion of MNPs. As biopolymers, they used chitosan, hyaluronic acid, bovine serum albumin, and gelatin, and as MNPs, they used magnetite nanoparticles prepared by the coprecipitation method. The morphology of the magnetic scaffolds was investigated using scanning electron microscopy (SEM), Fourier transform infrared spectroscopy (FTIR), X-ray diffraction, and energy-dispersive X-ray spectroscopy.
In vitro degradation analysis showed evidence of a slow degradation rate, and a biocompatibility test revealed no adverse effects on osteoblast cells. The mechanical properties of the scaffold were improved by increasing the MNP content.
Hyaluronic acid is a linear polysaccharide that can be found in many parts of the extracellular tissue
[141]. It can be used in hydrogel or solution form to repair different body sites because HyA is a part of the connective tissue with an essential role in lubrification, cell differentiation, and growth. Hydrogels from HyA can be easily produced due to functional groups such as alcohols or carboxylic acids. It is well known that innovative scaffolds can be made from HyA, and they exhibit biodegradable and bioactive properties, showing non-specific protein adsorption. These scaffolds are very effective in tissue repair and growth via cell receptors
[142]. Zheng et al.
[143] provided a comprehensive review of hyaluronic-acid-based materials used in bone regeneration. Composite hydrogel systems have proven their efficiency due to good mechanical properties, high biocompatibility, and biodegradability. They can also be combined with MNPs for drug delivery and an enhanced osteogenesis process. HyA stimulates extracellular matrix microenvironments, promotes cellular activities, and can realize crosslinking action with other polymers, and MNPs help deliver drugs or growth factors. Three-dimensionally printed HyA scaffolds have proven to have a strong influence on the bone formation process.
Proteins and peptides are derived from α—L amino acids. The main drawbacks of polypeptide- and protein-based materials consist of their lack of processability and immunogenicity, but good biological properties and low mechanical strength characterize these biopolymers. Collagen scaffolds are already implemented in clinical treatments, and some are in trials
[144]. Collagen degradation occurs as a result of two enzymes, i.e., collagenases and metalloproteinases, which produce an amino acid
[145]. Mechanical properties of type I collagen must be tuned. Its limited chondrogenic capacity and significant shrinking must be improved for use in scaffold manufacturing. Usually, collagen is combined with HyA, CS, or chondroitin sulfate
[146]. Collagen scaffolds are not used for load-bearing areas of the human body. Bianchi et al.
[147] investigated the nanomechanical properties of newly formed bone four weeks after implantation surgery. This was performed through magnetic scaffold insertion into the trabecular bone of rabbit femoral condyles. The developed magnetic scaffolds contain NdFeB magnets combined with HAp/Col, with MNPs directly nucleated on the collagen fibers in the manufacturing process or introduced later. It was concluded that the second production technique led to better results because the mechanical properties of the neo-bone had similar values to those of native bone. The addition of MNPs to the final product has an important influence on the osteogenesis process.
Through disintegration or denaturation, insoluble collagen results in a gelatin degradation compound. Gelatin has poor mechanical properties and a high biodegradability rate, and due to active chemical groups such as amino and carboxyl acids, the degradation time can be increased through different chemical treatments
[148][149]. Dashnyam et al.
[133] prepared a novel magnetic scaffold based on gelatin–siloxane for bone tissue engineering by incorporating magnetite magnetic particles using the sol–gel process. Porous scaffolds were manufactured based on the freeze-drying method. With the addition of MNPs, the mechanical properties were highly improved, the scaffolds exhibited superparamagnetic behavior, and the saturation magnetization increased directly proportionally to the MNP content. The developed implants showed good bone bioactivity. The rapid growth of the apatite minerals crystals and osteogenic differentiation were put in evidence. Cellular mineralization increased when MNPs were added.
Silk is a natural protein-based biopolymer characterized by good mechanical properties, a controllable degradation rate, and high biocompatibility. Silk fibers have high strength, good durability, low weight, and high elasticity. Silk is made from two proteins. The first is called fibroin, which consists of a fibrous portion; the second is named sericin, which is soluble in water and contains 18 amino acids
[150][151]. Samal et al.
[108] developed biomimetic magnetic silk fibroin protein scaffolds. These implants were intended to be used in magnetic-field-assisted BTE. MNPs were introduced into scaffolds through the dip-coating technique. Good magnetic hyperthermia, improved osteogenic effects, cell adhesion, and proliferation were reported.
2.3.2. Synthetic Biopolymers
Synthetic biopolymers are characterized by tunable properties and well-established structures and can be produced in different forms. They are much more easily manufactured than natural polymers but have a main drawback, i.e., bioinertia
[152]. Many modern synthetic materials have mechanical and physiochemical properties similar to those of human bone. The main classes of synthetic biopolymers include poly(α—hydroxy esters) (poly(ε—caprolactone) (PCL), polylactic acid (PLA), polyglycolic acid (PGA), poly(L-lactide-co-glycolide) (PLGA)) and poly(ethers) (poly(ethylene oxide) (PEO), polyvinyl alcohol (PVA), poly(ethylene glycol) (PEG), and polyurethane (PU)). These are the most used materials, and they have an imposed Young’s modulus, degradation rate, and mechanical strength. The abovementioned synthetic biopolymers exhibit different levels of biocompatibility, biodegradability, and mechanical properties, and no single material envisages all the ideal properties for scaffold manufacturing
[153].
Poly(ε—caprolactone) (PCL) is a biocompatible aliphatic and semicrystalline polymer that is very tough and hydrophobic
[154]. The initial degradation process consists of non-enzymatic bulk hydrolysis of ester connections that are catalyzed with the help of carboxylic acid end groups. PCL can induce foreign body responses, which are evidenced by the giant cells and the presence of macrophages. To increase its biocompatibility, solutions such as surface functionalization or a blended formulation must be considered. The rate of deterioration is relatively slow and can be longer than two years
[155]. Ganesh et al.
[156] incorporated a multimodal contrast agent with HAp nanocrystals inside a poly(caprolactone) nanofibrous scaffold produced through electrospinning. Magnetic resonance was used to analyze the scaffold’s influence on tissue regeneration. The implant biocompatibility was put into evidence through
in vitro tests with the help of human MSCs. Incorporating multifunctional hydroxyapatite nanoparticles (MF-nHAp) within the PCL nanofibers leads to the increased strength of the scaffold, good protein adsorption, proliferation, and differentiation of the cells. Dankova et al.
[109] developed a nanofibrous scaffold through electrospinning from PCL and MNPs. The biocompatibility of the scaffold was put into evidence by taking into account the biomaterial influence on fibroblasts and MSCs. When the MNP percentage increases, a more critical stimulation of cell adhesion, proliferation, and differentiation were noticed. A gradual rise in the saturation magnetization was observed, and it was concluded that up to 10% wt. MNPs, the effects were contained in the biological range. De Santis et al.
[110] used rapid prototyping (RP) technology to obtain 3D magnetic nanocomposite scaffolds made from a PCL matrix reinforced with iron-doped hydroxyapatite. It was noticed that by adding magnetic properties to biopolymers, an enhanced osteointegration process is obtained. Kim et al.
[128] studied a classical magnetic scaffold made of PCL and MNPs. MNPs were produced by a surfactant mediation process and distributed in the PCL matrix. Superparamagnetic behavior was observed, and it was concluded that the incorporation of MNPs leads to high hydrophilicity and water swelling of scaffolds. Using acellular apatite-forming ability tests, a high mineral induction potential of the implant was revealed. The mechanical stiffness increased directly proportionally to the MNP content, and high cell adhesion and proliferation were observed during
in vitro tests.
Unfortunately, PCL exhibits hydrophobic behavior, leading to reduced cell affinity and a low rate of tissue regeneration. To address this critical limitation, PCL can be combined with different polymers such as PLA or PLGA, and cell proliferation and adhesion can be improved
[157]. The synthetic polymer PLGA was approved by the Food and Drug Administration (FDA) for clinical use. Scaffold structures made from this material have been developed, which have proven to be efficient if they have an adequate porosity grade characterized by precise contour geometrical dimensions and internal morphologies, which sustain cellular attachment and structure colonization
[158]. In this case, the scaffold surface can be functionalized with bioactive substances or chemicals, and plasma treatment can be applied to increase implant efficacity. Chen et al.
[159] optimized the interaction between seed cells and scaffold to ensure beneficial conditions for cell growth under natural biomimetic conditions. They have reported the manufacture of a magnetic [PLGA/PCL] scaffold made using electrospinning technology and layer-by-layer assembly of superparamagnetic iron oxide nanoparticles. These composite scaffolds exhibited increased hydrophilicity and a high value of elastic modulus. They have a good influence on the osteogenesis process of stem cells. It was concluded that the magnetic properties of implants are a key factor in enhancing osteogenic differentiation, which is important as a bioactive interface between cells and scaffolds. The results were compared with those obtained in the case of gold nanoparticles, and the authors concluded that using MNPs in scaffold production leads to an increased osteogenic effect and a high application potential in BTE. Zhang et al.
[160] developed 3D MNPs combined with mesoporous bioactive glass/polycaprolactone ([MBG/PCL]/[Fe
3O
4]) composite scaffolds.
In vitro bioactivity, chemotherapeutic drug delivery, mechanical strength, and magnetic heating effect were put in evidence. The produced scaffolds had uniform macropores of 400 μm, a high porosity grade of 60%, and good compressive strength of about 14 MPa. The incorporation of MNPs did not disturb the apatite mineralization process but provided the scaffolds with a high magnetic heating ability and enhanced osteogenesis-related gene expression. The authors concluded that these medical devices are essential in cancer therapy, and they can also stimulate new bone formation and angiogenesis.
PLA is a semicrystalline polymer with high biocompatibility, hydrophobic properties, biodegradability, and easy processability
[161]. The degradation products that result are carbon dioxide and water, which are not harmful to the human body
[162]. This polymer can be used in clinical practice as poly(L-lactic acid) (PLLA), poly(D,L-lactic acid) (PDLLA), and poly(D,L-lactide) (PDLA). Shuai et al.
[158]. elaborated a PLLA/PGA scaffold made using the laser sintering method incorporated with Fe
3O
4 magnetic nanoparticles. A rigid enhancement effect of MNPs was put in evidence through an increase in compressive strength and modulus of about 70%. After
in vitro and
in vivo tests, the obtained results indicated enhanced angiogenesis and osteogenesis effects, fibrous tissue formation, and new bone development.
PGA is a linear aliphatic polyester not soluble for organic solvents because it has a high degree of crystallinity. PGA can break into glycolic acids, which can be combined with the tricarboxylic acid cycle, and expel products such as water and carbon dioxide
[163]. PLGA is a well-known ring-opening copolymer of PGA and PLA that is biodegradable, has a low toxicity level, good mechanical properties, a controllable degradation rate, and favored cell adhesion and multiplication. In the BTE domain, PLA, PGA, and PLGA are used for scaffold manufacturing to restore the function of damaged organs or tissues. The FDA has already approved PLA and PGA uses for different medical implants due to the safe elimination process of lactic and glycolic acid secondary products
[164]. Jia et al.
[165] developed a scaffold for oral bone defect restoration. Three-dimensional composite scaffolds made of PLGA and superparamagnetic iron oxide nanoparticle coatings were implanted in rat animal models to analyze the palate–bone regenerating effects and their interaction with the oral microbiota. These special MNP-coated implants induced an excellent bone regeneration effect. Regarding oral bacteria, a decrease in the
Clostridium spp. population and a dominant flora consisting of
Proteobacteria were put in evidence. Although MNPs had a beneficial effect on bone regeneration, they altered the oral microbiota in rats. MNPs upregulated hepcidin and the concentration of iron serum.